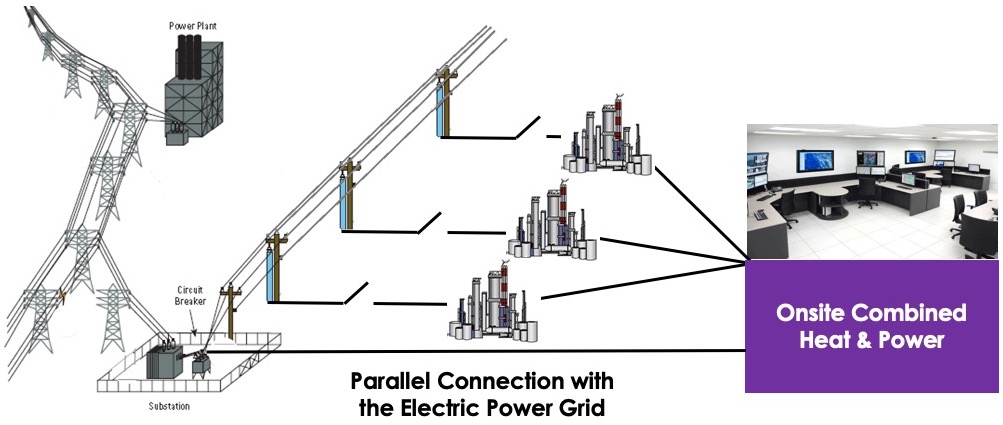
PowerIn is aggregating proven reliable technology to finance, design, build, own and operate onsite combined heat and power plants that primarily serve natural gas processing plants located within rural areas of North America. Each distributed onsite project is to include n+1 redundancy (99.9% reliable) and are to be controlled from a centralized cyber secure command center.
For rural areas that have a suitable electric power grid, PowerIn’s generation facilities will interconnect with the local utility grid to support the supply of electric power to the surrounding community. In this scenario the connected power grid also provides additional back-up to PowerIn’s onsite primary generation, thereby further improving redundancy to n+2 (99.999% reliability).
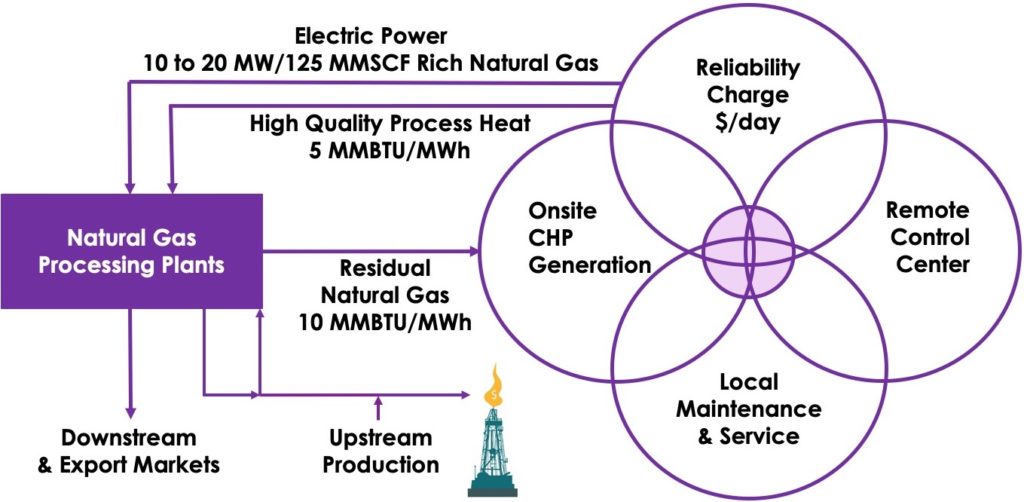
Processed natural gas offers a low cost, environmentally friendly opportunity for onsite production of energy. PowerIn is establishing the capability to convert abundant supplies of residual natural gas into resilient, reliable, high quality electric power and heat within rural areas of North America where oil and gas is produced.
On average, PowerIn’s combined heat and power facilities have the potential to divert greater than 5 million BTUs of natural gas from either flaring or from its use onsite, within natural gas process boilers, for every 1 million watt hours of electricity required to process incoming rich natural gas.
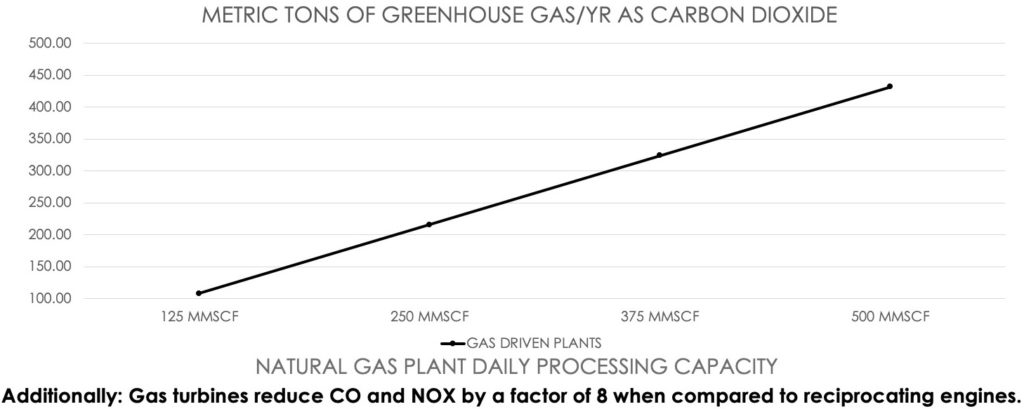
Potential for the reduction in greenhouse gas emissions is directly dependent upon the amount of natural gas that can be diverted from either flaring or from its use within processing plant reboilers to produce electricity that historically is supplied by the local power grid. PowerIn’s facilities should be capable of recovering at least 85% of the associated heat value (~ 10 MMBTU/MWh) of natural gas consumed onsite for the generation of power and heat.
The U.S. Energy Information Administration (EIA) reports that 53.07 kg of greenhouse gases are emitted as CO2 for each 1MM BTU of natural gas burned. While the Permian Basin Petroleum Association states that the electric power demand for 80% of the natural gas processing plants within the Permian requires a minimum of 240 MWh for every 125MM cubic feet per day of processed rich gas.
Therefore, the minimum potential reduction in annual greenhouse gas emissions for these gas driven processing plants would equate to 8.5 x 240 x 53.07/(1000kg/metric ton) = 108 metric tons for each increment of 125MM cubic feet of rich gas processed per day.
Additionally, the use of gas turbines instead of reciprocating engines reduce carbon monoxide and nitrous oxide emissions by a factor of eight, assisting natural gas plants with multiple processing trains to stay below federally mandated Title V emission limits.